by Allan Ung
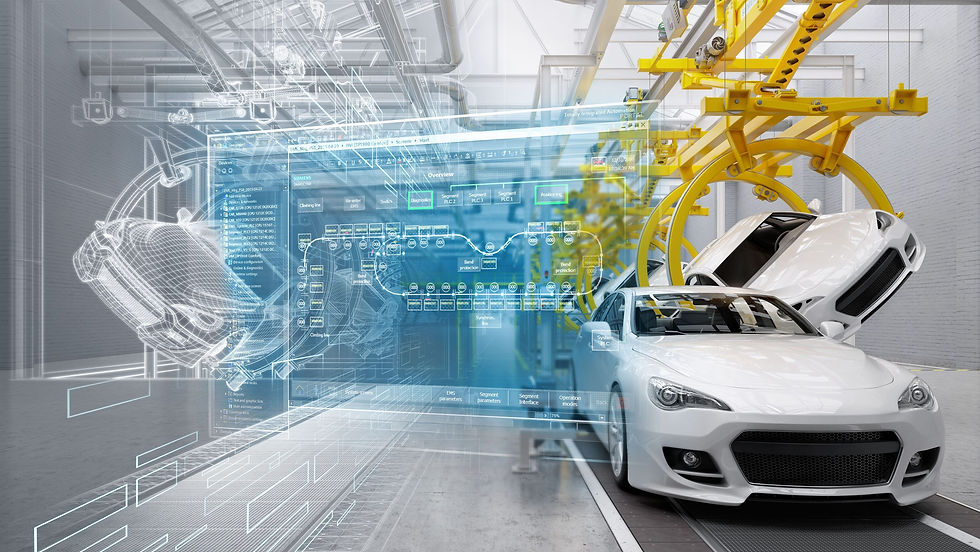
Recession or boom, companies need to sharpen their competitive edge by applying Lean Management principles to cost reduction - that is, the elimination of non-value-added activities or waste from the value stream processes.
Be Lean
In the Lean Management philosophy, all activities in an organization are grouped into two categories:
1. Value-added (VA) activities, and
In the context of Lean Management, VA and NVA activities are viewed from the customer perspective.
VA activities are those that bring higher value to products and services. Examples are answering customer queries, entering orders, ordering materials, laying foundation, creating codes, assembling parts, shipping of goods to customers, etc.
Customers are willing to pay for these improvements which can change the form, fit or function of a product or service.
On the other hand, NVA activities are tasks that do not increase market form or function.
Examples are filing, copying, recording, waiting, counting, checking, inspecting, testing, reviewing and obtaining approvals. These activities should be eliminated, simplified or reduced as much as possible.
By tackling waste from an end-to-end business process, not only can your company improve the value of its products and services, you can also achieve significant cost reduction, strengthen cash flow and emerge from the downturn with a stronger and more competitive profile.
Eight Types of Waste
There are eight types of waste in a manufacturing environment.
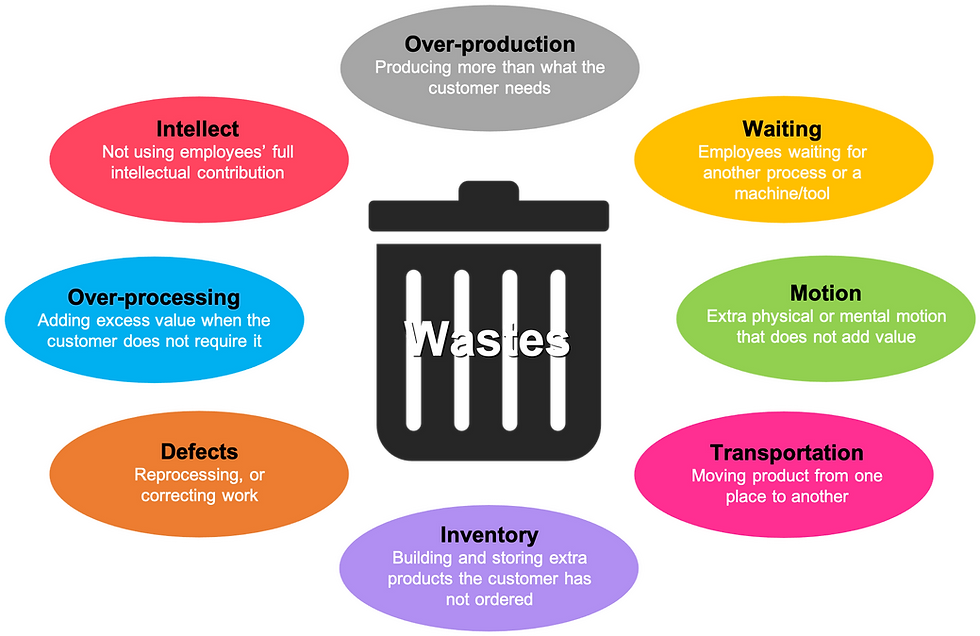
Eight types of lean waste
Studies have shown that in a typical organization, some 90% or more of all activities fall into the NVA bucket.
Although the explanations and examples provided below may be more relevant for manufacturing industries, the concepts can be universally applied to service industries as well.
The eight types of waste are:
1. Waiting – This is the idle time resulting from waiting for materials and information, email queues from customers, delayed shipments, lot processing delays, capacity bottlenecks, unbalanced workload, long setup times, equipment or system downtime and so on.
2. Over-Processing – This results from unnecessary procedures due to undefined customer requirements, lack of effective communication, product changes without process changes, redundant approvals, making extra copies and excessive reporting.
3. Defects – These are errors, mistakes, scrap, rework, replacements, re-inspection and re-testing. The causes are incorrect data entries, poor quality, weak process control, inadequate training, deficient planned maintenance and customer needs that were not understood.
4. Excess Motion – Refers to any movement of people or machine that does not add value to the product or service. Common causes are poor plant or office layout, double handling, inconsistent work methods and poor workplace organization.
5. Transportation – This refers to the transporting of parts, materials and files or documents around the plant or office. The causes are poor plant or office layout, widely spaced equipment and workstations and poor understanding of the process flow.
6. Over-Production – This happens when you make too much, too early and faster than is required by the next process. The causes include unclear goals, excessive lead times, and outdated forecasts. Tip: You should reduce your batch size to match the rate of demand. Produce exactly to customer demand, not more.
7. Excess Inventory – This happens when you have more inventory than is needed for a job. It is important to tackle excess inventory as it has a huge impact on cash flow. Tip: Review your materials purchasing strategy – where can you buy them at a cheaper price, in smaller amounts and can be delivered to you more frequently?
8. Intellect - This refers to not utilizing the time and talents of people. Examples are not engaging or listening to employees in finding solutions; lack of information or best practice sharing across the organization; mismatched work functions with skill sets.
Eliminate the Waste
The ability to find waste in your organization is the first step towards their elimination.
The next step is to set up problem solving teams and enable them to reduce or eliminate the waste. A common problem solving technique is the PDCA (Plan-Do-Check-Act) approach.
Involve your employees in problem solving or process improvement. If they know that they are an active part of the solution, they can identify sources of waste or savings that you might not be aware of.
Do note that not all waste is of equal importance. You will need to identify the “right waste”– those that have the greatest impact on the business case or bottom line.
Continuous Process
For waste elimination to be successful and sustainable, an organization’s senior executives need to adopt a mindset that cutting waste to cut costs is an on-going journey of continuous improvement.
It has to be a collaborative effort between management and employees.
A common mistake for senior executives to avoid is to treat waste elimination as another one-off “tool” or quick fix.
It is essential to manage waste elimination as a strategic change initiative that is aligned to the organization’s purpose, encompassing both people and process transformations.

Article by Allan Ung, Principal Consultant at Operational Excellence Consulting, a distinguished management consultancy based in Singapore. Our firm specializes in maximizing customer value and minimizing waste through the strategic adoption of Design Thinking and Lean management practices. For further details, please visit www.oeconsulting.com.sg