Lean Management Assessment: Is Your Business on the Path to Operational Excellence?
- Allan Ung
- Feb 14
- 3 min read
Updated: Mar 20
Allan Ung
In the pursuit of operational excellence, organizations often seek tools that can assess their progress and guide their improvement efforts effectively. One such tool that stands out is the Lean Management Assessment (LMA). Developed from the principles of Lean thinking, the LMA offers a structured and practical approach to evaluate and enhance your Lean implementation, providing invaluable insights and guidance for continuous improvement and sustainable progress.
Benefits of Assessment
1. Clarifying Goals: The dimensions and questions in the assessment help clarify what you are working toward, both personally and for your organization.
2. Status Check: It provides a clear picture of your current standing relative to your standards and past performance.
3. Identifying Improvement Opportunities: The results of the assessment help pinpoint areas needing improvement, guiding your efforts effectively.
The Framework
The Lean Management Assessment framework, adapted from "Creating A Lean Culture" by David Mann, stands out as a simpler, more practical alternative to the Shingo Model and the Baldrige Excellence Framework.
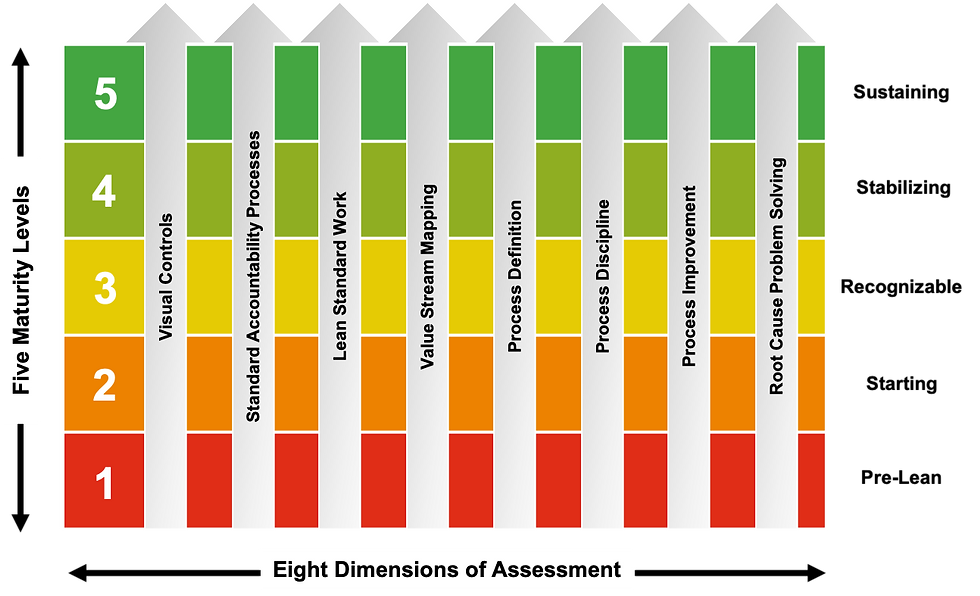
Lean Management Assessment Framework
It covers eight dimensions or categories and defines five levels of maturity, providing a comprehensive view of your Lean management implementation:
1. Visual Controls: Reflect the actual vs. expected pace or progression of work, and capture delays or interruptions that arise during work.
2. Standard Accountability Processes: Convert problems/opportunities noted into task assignments for cause analysis or corrective action.
3. Lean Standard Work: Reflect process focus and include regular reviews of visuals, accountability, and follow-up on improvements.
4. Value Stream Mapping: Show the step-by-step movement of information, patients, or materials through an area, and communicate process performance measures and improvement plans.
5. Process Definition: Documented definitions of all line and support processes, with current documentation that matches actual practice.
6. Process Discipline: Adherence to defined processes and tasks, with actual practice reflecting disciplined adherence.
7. Process Improvement: Involvement of everyone in process improvement, from line workers to executives, with a focus on improvements from small to large in scope.
8. Root Cause Problem Solving: Problem-solving focused on eliminating the source of a problem, with leaders asking "Why?" and initiating data-based root cause problem solving.
Scoring System
The assessment uses a 5-point scale (1=minimum, 5=maximum) to rate each dimension or category. The scoring can be conducted by a single assessor or a team, providing flexibility in the assessment process. The five levels of maturity ("Pre-Lean," "Starting," "Recognizable," "Stabilizing," and "Sustainable") allow you to track your progress and identify areas for improvement effectively.
1. Pre-Lean: No or minimal implementation of Lean practices.
2. Starting: Initial steps taken towards Lean implementation, with sporadic adherence to Lean principles.
3. Recognizable: Lean practices are noticeable and consistent, but not yet fully ingrained in the organization.
4. Stabilizing: Lean practices are well-established and consistently applied, leading to stabilization of processes.
5. Sustainable: Lean practices are fully integrated into the organization's culture, leading to continuous improvement and excellence.
Assessment Guidelines
1. Conduct assessments on the floor through direct observation and engagement with employees.
2. Use a format that lists criteria by maturity level for each dimension to guide observations.
3. Assess regardless of your Lean journey stage, establish an assessment schedule, and keep the process simple.
4. Utilize a calibration method, starting with direct reports, and consider a mixed model for large organizations.
5. Look at assessment scores as a profile rather than a single average value and use radar charts for interpretation.
Conclusion
In conclusion, the Lean Management Assessment offers a structured and insightful method to evaluate and improve your Lean implementation. By providing clear insights and guidance for progress, it serves as a valuable tool for organizations committed to achieving operational excellence.
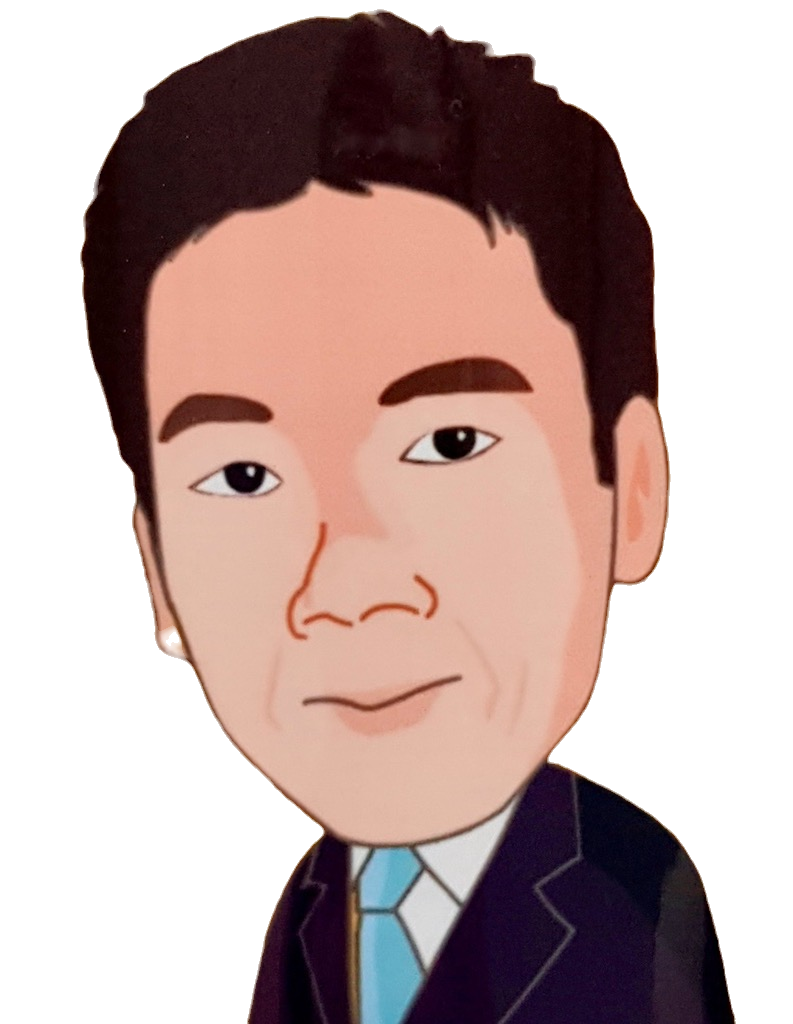
Article by Allan Ung, Principal Consultant at Operational Excellence Consulting, a distinguished management consultancy based in Singapore. Our firm specializes in maximizing customer value and minimizing waste through the strategic adoption of Design Thinking and Lean management practices. For further details, please visit www.oeconsulting.com.sg
Comments