
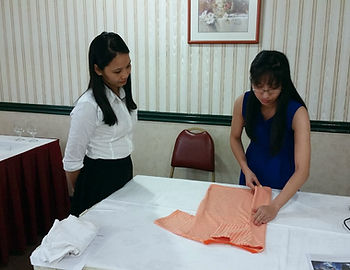
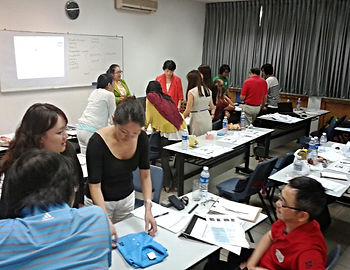

Training program:
TWI Program:
Job Methods (JM) Training
Description
The TWI Job Methods (JM) program teaches supervisors how to improve methods for producing greater quantities of quality products in less time by effectively using available workforce, machines and materials. Participants are taught how to break down jobs into their constituent operations. Every detail is questioned in a systematic manner to generate ideas for improvement. New methods are developed by eliminating, combining, rearranging, and simplifying steps in the process. Job Methods yields significant benefits including reduced cost through productivity gains, increased throughput, and reduced work in process.
NOTE: Our TWI training materials are closely aligned to the original TWI training manuals developed by the TWI Service.
Recommended Audience
-
This course is designed for any manager, supervisor, line leader and trainer wishing to gain practical know-how on the principles, process and tools of the TWI Job Methods methodology to enhance Lean transformation
Methodology
-
This is an experiential workshop, which emphasises engagement, interaction and practice
-
Participants should expect short presentations that introduce content, examples, video presentations, group activities for skills practice, and group discussions for reflection that deepens their learning
-
Hands-on practice demonstrations by participants on the four-step job improvement process and the Job Breakdown Sheet for Work Analysis
-
Training curriculum based on the original TWI training manuals developed by the TWI Service
Learning Objectives
-
Improve job methods based on the 4-Step Process for JM
-
Apply the Job Breakdown Sheet to analyze the current method and develop the new method
-
Utilize the JM Improvement Proposal Sheet to communicate and gain buy in to the new method
Outline
-
Introduction to TWI - JM
-
Definition of a Supervisor
-
5 Basic Needs of Supervisors
-
Demonstration Job: Current Design & New Design
-
4 Steps for Job Methods Improvement
-
Step 1 – Breakdown the Job
-
Job Breakdown Sheet (JM)
-
-
Step 2 – Question Every Detail
-
5W’s & 1H
-
-
Step 3 – Develop the New Method
-
Eliminate, Combine, Rearrange & Simplify
-
Principles Under Simplify
-
JM Improvement Proposal Sheet
-
-
Step 4 – Apply the New Method
-
Examples of Ideas for Improvement
-
Practice Demonstrations – Job Breakdown for Present & Proposed Methods
-
-
Managing Resistance & Resentment
-
Review of 4 Steps for JM
-
Summary & Closing Comments
Award of Certificate
-
Certificate of Attendance will be issued to participants who have attended at least 75% of the workshop
Duration
-
1 day