Training
Within
Industry
(TWI)
Building stability and consistency through skill development.

TWI: The Missing Link in Lean
What is TWI?
The Training Within Industry (TWI) programs were developed by some of the most renowned training and management experts in the United States, and were rigorously tested in the field before being released to the public. When the TWI programs were introduced to Japan in the early 1950s, many Japanese companies enthusiastically adopted them and their underlying principles. Toyota was one such company.
The TWI programs are a critical component of Lean methodology, with the goal of developing a more skilled workforce, improving labor and management relations, enhancing productivity, and fostering a culture of continuous improvement. The TWI programs are the foundation of the Toyota Production System that we know today.
At the heart of the TWI programs are three "J" or "Jobs" programs: Job Instruction (JI), Job Methods (JM), and Job Relations (JR). These programs focus on instructing individuals on the best methods for performing their jobs, continuous improvement, and enhancing communication and leadership skills.
The Five Needs Model

Key Role of Supervisors
Supervisors play a crucial role in any organization as they are responsible for overseeing the work of others and ensuring that the work is completed efficiently and effectively. To fulfil their responsibilities, supervisors must have a deep understanding of their job, responsibilities, and possess various skills.
The Training Within Industry (TWI) program provides a framework for supervisors to develop the necessary knowledge and skills to be successful on the job.
The Five Needs Model for Good Supervisors is a fundamental concept in the TWI program, which outlines the five needs that must be satisfied for supervisors to be effective in their roles. The first two needs in the Five Needs Model focus on acquiring knowledge, while the last three emphasize the development of skills.
Knowledge is obtained through reading or attending classes, while skills are learned through practice and repetition. To effectively apply the TWI program, acquiring knowledge about it must be accompanied by developing the necessary skills through practice.
TWI Methodology
TWI programs follow the Four-Step Learning Process developed by Charles Allen as described in the table below.
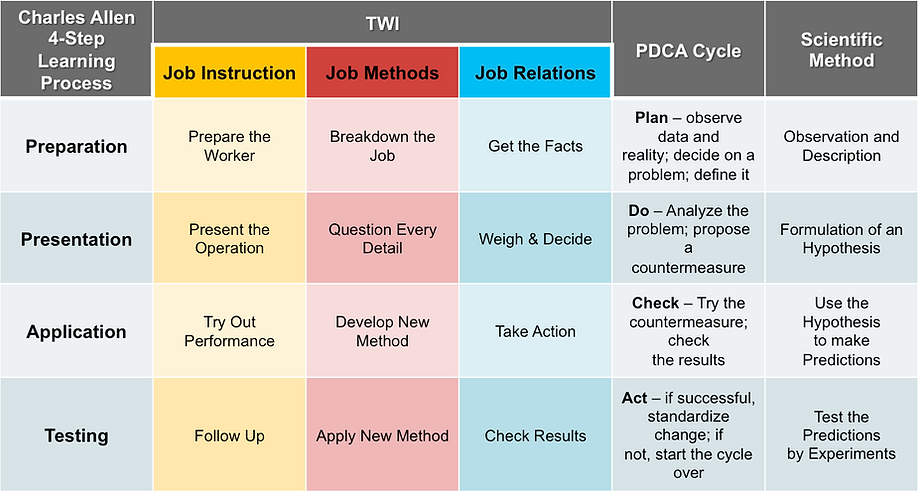
All TWI programs are designed to be simple, follow a blueprinted procedure, adopt a learn by doing principle and finally achieve the multiplication effect through a training cascade.
Companies that have implemented TWI have reported improvements of 25% and more in increased production, reduced training time, reduced scrap and reduced labor-hours.
Since 2009, Operational Excellence Consulting has helped various companies in the South-East Asian region to develop their TWI capability. The companies that we have helped include NSG Group (Vietnam), Transitions Optical (Philippines), Aprati Foods (Cambodia) and Wow Education (Singapore).
Learn how to apply the TWI Training Programs (JI, JM & JR) to improve workplace productivity, quality and safety.
Learn how to instruct employees so they can quickly remember to do a job, correctly, safely and conscientiously.
Learn how to improve methods for producing greater quantities of good quality products in less time by effective use of current resources.
Learn how to lead employees so that problems are prevented and analytical methods are used to effectively resolve problems.
Our TWI Workshops Around the Region
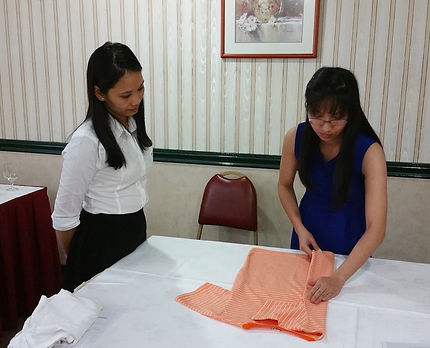
TWI Train-the-Trainer program
(JI, JM & JR) in Singapore

TWI Job Instruction workshop
in Ho Chi Minh City, Vietnam

TWI workshop (JI, JM & JR)
in Kep, Cambodia

TWI workshop (JI, JM & JR)
in Manila, Philippines

TWI Job Instruction workshop in Singapore
Client Success Story
WORKSHOP HIGHLIGHT
August 13, 2015